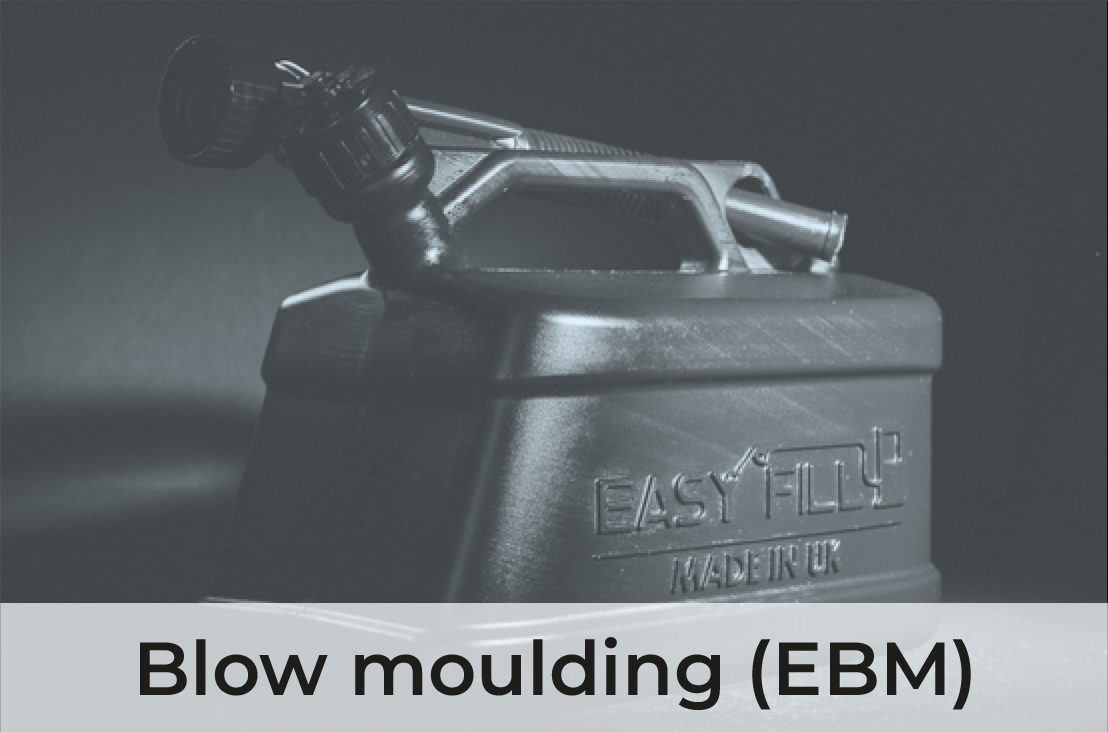
Blow Moulding
Extrusion Blow Moulding (EBM)
Extrusion blow moulding is a process of producing hollow plastic parts by melting plastic resin and extruding the plastic into a mould tool. Once the plastic is extruded through the machine it flows between the open two halves of a mould tool, which then shuts the plastic inside. The pressurised air is then pushed into the mould to form the shape of the tool cavity inside. Once it cools the mould is opened releasing the part so the process can be repeated.
EBM can be used for virtually any thermoplastics; from PP, HDPE, ABS, HIPS PA6 to PETG. It allows for a high rate of production with relatively low tooling cost and can incorporate design features such as handles and co-extrusion/multilayers.
Injection Stretch Blow Moulding (ISBM)
It has always been our business to ensure we are meeting the needs of our customers and one key area we have identified is the manufacturing of injection stretch blow moulded parts. ISBM is a combination of injection moulding and blow moulding to produce very high quality and very high clarity precision bottles and containers.
First a preform is created via the injection moulding process; the preform is then placed in the ISBM machine and heated before being placed in the blow tool cavity.
The mould shuts and high-pressure air is injected where it stretches the preform vertically inside before being blown to fill the cavity. Once the blow cycle ends the tool opens to allow another preform to be loaded and the process can start again.